1范围
2规范引用文件
3术语和定义
4汽车前后防撞梁总成主要功能
5 汽车前后防撞梁总成性能
5.1 汽车前防撞梁总成碰撞性能概述
5.2 汽车后防撞梁总成碰撞性能概述
5.3低速碰撞对前防撞梁设计的性能要求
5.4高速碰撞对前防撞梁设计的性能要求
6汽车前后防撞梁总成设计要点概述
6.1满足市场法规和标准
6.2整车碰撞对汽车前后防撞梁的布置要求
6.3汽车前后防撞梁总成结构形式
6.4前防撞横梁结构形式
6.5后防撞横梁结构形式
6.6吸能盒设计要求
6.7前拖车钩结构设计要求
6.8防撞梁和车身连接标准件选用
7 防撞梁总成设计经验
8 总结
9 参考文献
1范围
该规范适应于M1类车辆汽车前后防撞梁的设计。主要介绍了汽车开发过程中汽车前后防撞梁总成的作用及在整车中的影响。首先对汽车前后防撞梁在整车中的功能进行了概述,尤其是对汽车前后防撞梁碰撞性能做了详细的描述;同事对汽车前后防撞梁总成设计要点作了描述;最后对汽车前后防撞梁的加工制造型作了阐述。
2规范引用文件
下列文件中的条款通过本规范的引用而成为本规范的条款。凡是注日期的引用文件,其随后所有的修改单(不包括勘误的内容)或修订版均不适用于本规范,然而,鼓励根据本规范达成协议的各方研究是否可使用这些文件的最新版本。凡是不注日期的引用文件,其最新版本适用于本规范。
GB 11551-2003 乘用车正面碰撞时的乘员保护
GB 17354-1998 汽车前、后端保护装置
GB 20072-2006 乘用车后碰撞燃油系统安全要求
C-NCAP 中国新车评估程序2012版
3术语和定义
汽车前后防撞梁总成是车身第一次承受撞击力的装置, 汽车在发生碰撞时传递能量,同时吸能盒被压溃而吸收能量,从而保护乘员及行人,最终满足车辆法规要求。
4汽车前后防撞梁总成主要功能
汽车前后防撞梁总成,是车身第一次承受撞击力的装置,也是车身中的一个重要构件,其功能主要有:
(1)保护保险杠在低速碰撞过程中尽量不要破裂或者发生永久变形。
(2)保护车身骨架前后端纵梁在行人保护或可维修性碰撞时不发生永久变形或者破裂。
(3)在100%正面碰高速撞、后面高速碰撞时起到第一次的吸能作用,在偏置碰撞中不仅起到第一次吸能作用,还能起到碰撞过程中均衡传递受力的作用,防止车身左右两侧受力不均。
5 汽车前后防撞梁总成性能
5.1 汽车前防撞梁总成碰撞性能概述
前防撞梁总成的碰撞性能主要需满足低速碰撞和高速碰撞两个部分的法规要求。其中,低速碰撞需满足的法规要求为:GB 17354-1998 汽车前、后端保护装置。 高速碰撞需满足的法规要求为: GB 11551-2003 乘用车正面碰撞时的乘员保护;C-NCAP标准,需满足其100%正面碰撞和40%偏置碰撞要求。
5.2 汽车后防撞梁总成碰撞性能概述
后防撞梁总成的碰撞性能主要需满足低速碰撞和高速碰撞两个部分的法规要求。其中,低速碰撞需满足的法规要求为:GB 17354-1998 汽车前、后端保护装置。高速碰撞需满足的法规要求为:GB 20072-2006 乘用车后碰撞燃油系统安全要求。
低速碰撞对后防撞梁设计的性能要求:后防撞梁总成需满足的低速碰撞性能要求同前防撞梁总成。
高速碰撞对后防撞梁设计的性能要求:国标GB 20072-2006规定:碰撞器撞击表面应平坦,高度不小于800mm,撞击器表面下边缘至地面的间隙应为175±25mm,后防撞梁对后碰的主要贡献为利用吸能盒的压溃变形吸收能量,缓解碰撞刚性变形,保证燃油箱周围安全的变形空间。因此在设计后防撞梁及吸能盒时,需综合考虑下面三方面:
(1)、保证基本的许可变形量。许可变形量,决定了碰撞过程中的平均减速度。汽车的纵向变形量与平均减速度是成反比的。平均减速度作为汽车结构耐碰撞性的主要设计指标,在设计开始阶段就必须综合考虑确定。
(2)、保证基本的许可变形空间。保证许可变形空间是指汽车在发生碰撞后,变形区域不会对乘员和危险部件(如油箱、燃汽罐)形成威胁和伤害,而且包括后部许可变形区域内的塑性变形不会导致在碰撞过程中车门打开、碰撞后车门锁死等状况发生。
(3)、调整截面形状(通过吸能筋与加强筋的布置)、厚度、尺寸和结构形式等使结构的变形阻力保持在适当水平,并重视局部弱化使整车刚度分配符合设计原则及能量吸收曲线图,增大撞击吸收能量的腔型结构。
5.3低速碰撞对前防撞梁设计的性能要求
低速碰撞的国家标准GB l7354—1998规定的正撞速度为4km/h,车角碰撞速度为2.5 km/h,对车身的要求就是车身本体、前防撞梁和吸能盒等不能有任何损坏,最好前保险杠也不能破裂或者发生永久变形。
在国外,从事汽车保险业务的保险机构,一般采用15km/h的碰撞试验来模拟最常见的可维修碰撞,试验的目的是要求尽量减少零部件的损坏以减少维修和保险费用。具体来说,一般要通过合理设计将损坏零件控制在翼子板、发动机罩盖、前保险杠系统、前格栅、前大灯等外表面零件和部分骨架件,比如前防撞梁以及吸能盒等零件范围内。车身零体,特别是纵梁不能产生任何变形。当然最好大灯支架、水箱上横梁等零件不要损坏,即使损坏,也要便于修复。在可维修碰撞中,合理设计传力路径是非常重要的,重点来说说汽车防撞梁吸能盒的设计
(1)将吸能盒设计成和纵梁在同一轴线上,避免产生弯曲变形。
(2)在吸能盒上预设一些压溃筋,以便让吸能盒在轴向上发生压溃进而吸收所有能量,从而不对包括前纵梁在内的车身本体产生损害。
(3)将这些容易损坏的部分骨架件,如前防撞梁和吸能盒设计成用螺栓和车身本体联结的可拆卸结构,为减少维修和保险成本。
5.4高速碰撞对前防撞梁设计的性能要求
目前设计上普遍接受和采用的是将车身分为前中后3个吸能区,其中前吸能区主要由前防撞梁和吸能盒组成,利用强韧的吸能材料尽可能多地通过变形吸收因撞击产生的巨大能量,同时利用结构上的受力连续进行左右分流并将能量向后面传递。中吸能区主要由前纵梁和副车架组成,通过合理变形来吸收大部分能量。后吸能区主要为高强度和刚度的驾驶舱,设计上通过避开可能发生对乘员不利的危险变形,减少正面碰撞导致的对驾驶舱的侵入和保持相对较低的碰撞减速度,以此保证乘员的安全。前中后3个吸能区是设置正面碰撞多层传力路径的基础,设置正面碰撞多层传力路径的目的也就是为体现3个吸能区的优势,使能量能合理有效地吸收和传递。正面碰撞多层传力路径一般是3层。
正面碰撞3层传力路径一般分为上中下3层,正面碰撞传力路径上层是由发动机舱上纵梁和前悬塔状形罩板等零件组成,吸收了部分从前部传来的碰撞能量并把其余能量向A柱和前围及其加强梁进行分散传递。中层主要是由前纵梁组成,也包括了前防撞梁和吸能盒等,是主要的传力路径。前防撞梁和吸能盒将接受到的碰撞能量进行左右分流和初步吸收,并通过它们将能量往前纵梁延伸板、门槛、中央通道等分散传递。下层主要是由前副车架组成,吸收了部分从前部传来的碰撞能量并把其余能量向前纵梁延伸板和门槛等分散传递。
6汽车前后防撞梁总成设计要点概述
6.1满足市场法规和标准
汽车前后防撞梁总成设计,主要是根据市场法规和标准来定义前防撞梁总成的性能。如:法规前碰ODB的定义、汽车前后防撞梁低速碰撞吸能、压溃空间、C NCAP试验ODB碰撞标准、整车性能等。为满足这些要求,我们需要对汽车前后防撞梁的碰撞性能的敏感性,如:汽车前后防撞梁的布置高度、结构、压溃空间、截面面积、材料等进行研究。
6.2整车碰撞对汽车前后防撞梁的布置要求
汽车前后防撞梁的布置高度由前纵梁的高度来决定,如果此高度匹配不合理会导致前纵梁在碰撞过程中压溃失稳,导致前纵梁后端大弯曲变形很可能对乘员舱侵入量过大。
汽车前后防撞梁的安装位置,除需满足上述碰撞要求的相容性原理,即两车发生正面相撞时,不合适的防撞梁高度既保护不到自身,还会对对方车辆造成巨大伤害;还需要根据车身高度,轮毂直径的大小来综合评定,并没有一个明确的标准。一般车型的安装高度在400-500mm左右,但如果超过520mm,则会对C NCAP等相关碰撞试验的成绩造成影响。
保证与周边件间隙≧10mm。前防撞梁总成一般是螺接到机舱纵梁上,误差积累大,同时车身前端安装有很多子件,故要求前防撞梁总成与周边件的间隙在10mm 以上。
在X 向预留出70mm 的行人保护缓冲空间。
6.3汽车前后防撞梁总成结构形式
标准的汽车前后防撞梁总成一般由防撞梁本体和吸能盒组成,部分车型还包含拖车钩螺纹管,为降低维修成本,防撞梁一般采用螺栓连接固定在车身上。
6.4前防撞横梁结构形式
前防撞横梁的结构主要有四种方式:冷冲压不同技术对应的优化断面,有不同程度的差别。
冷冲压拼焊的前防撞横梁(见图1)保持了与车身其它钣金相同的制造技术,不需要单独生产线,故制造成本低廉,不足在于重量大,不便于车身轻量化。通常材料选用HC420/780DP或HC550/980DP,具体结构、材料根据车型差异及CAE分析相应选择。
辊压成形的前防撞横梁(见图2),需要一条专用辊压线,其断面为箱体结构,类似双层板,重量方面优势不大。通常材料选用HC420/780DP或HC550/980DP,料厚1.8mm,具体根据车型差异及CAE分析相应选择。根据目前供应商制造工艺限制,目前合理的防撞梁半径R≥2700mm。
热冲压的前防撞横梁(见图3),需要一条专用热成形加工线及专用模具,模具需有专用冷却管道(见图4),综合成本较高,优势在于重量轻。
铝制的前防撞横梁,需要专用设备及工装,综合成本较高,优势在于重量轻。
6.5后防撞横梁结构形式
后防撞横梁的制造主要为冷冲压和铝制,冷冲压横梁一般为U形截面结构,通常材料选用HC250/450DP、HC340/590DP,具体形状、材料根据车型差异及CAE分析相应选择。
6.6吸能盒设计要求
吸能盒主要为箱体结构,常与连接板焊接成一个整体(见图5),吸能盒上一般需布置2至3条吸能筋,主要目的是便于低速碰撞时吸收足够的能量,保证车身本体不被破坏。同时设计吸能筋时需遵循以下4条原则:
(1)加强筋的轴线必须垂直于受力方向,否则在振动时会引起扭转;
(2)必须沿支撑之间最短距离布置;
(3)采用交叉筋时,应考虑在交叉点容易产生应力集中,相对减小了交叉点的刚性,所以在交叉点要注意圆角过渡,圆角半径应大于筋的宽度的两倍;
(4)加强筋的形状在平的或稍凸起的零件上,加强筋应沿零件对角线布置,在深弯曲的零件上应垂直于零件的弯曲轴线。
定义防撞梁本体和吸能盒截面尺寸:Z 向高度、Y 向宽度、X 向长度: A 级车型吸能盒在X 向长度一般在120mm 左右,A0 级车型长度约在100 mm。横梁本体X 向截面尺寸受吸能盒和保险杠位置所限制,故不能取值太大,一般在55mm。可以根据钣金材料级别、整车受力大小和整车安全星级等综合因素而调整。
吸能盒Z向高度、Y向宽度与纵梁截面基本一致,偏差不大于5mm。吸能盒和纵梁中心轴线一致。
6.7前拖车钩结构设计要求
前拖车装置工作方式(如:螺接、挂钩)和布置位置;一般前拖车装置采用螺接方式。布置位置,理论上希望拖车装置对称中心线与机舱纵梁中心重合,或偏离距离越小越好。如下图所示,前拖钩安装位置主要有四种:机舱纵梁、吸能盒中心、横梁内部、横梁边缘。

更多车身设计资料分享,加启飞汽车设计微信qifei1799
感谢大家对启飞汽车设计支持,现添加启飞汽车设计官网微信qifei1799。提“老杨”即可获得关于:车身、内外饰、底盘、总布置、整车CAE、catia参数化、catia、产品设计(家电、医疗器械、通信设备)、四大工艺、整车逆向开发、造型、模具设计、新能源三电 等相关领域等核心资料。
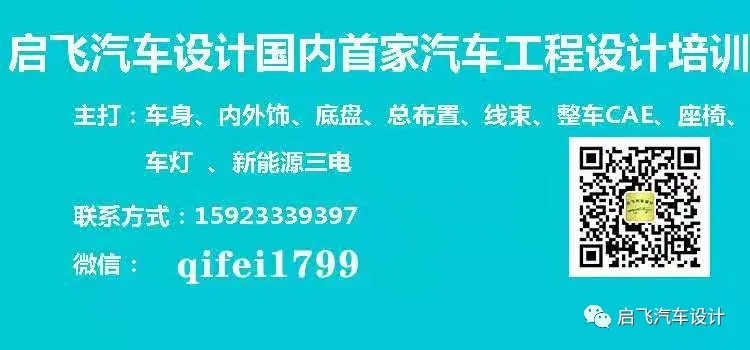