启飞汽车
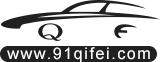
启飞汽车设计汽车设计— 国内专业产品设计培训基地!咨询热线:+86-15923339397
为中小型企业汽车研发和制造提供解决方案
专业承接整车设计开发项目
为各大主机厂,高校提供专业专项培训
为设计爱好者、毕业生提供专业系统培训
2018-08-22151作者:启飞汽车设计
摘要
在卡车的总装过程中, 整车不同部位零部件的结构、工作形式和动静态载荷存在差异, 未结合实际的通用螺栓扭矩控制方法, 易造成特殊部位螺栓扭矩失效, 难以保证整车可靠性, 因此需对不同部位零部件的扭矩控制方式采取不同的控制方案。文中介绍了在解决总装螺栓扭矩偏差过程中, 通过分析、验证, 总结出来的一套螺栓扭矩偏差的控制方法;实际运用表明, 该方法能保证整车装配过程螺栓扭矩均符合技术要求, 从而达到提高整车可靠性的目的。
一、目前车辆生产过程中螺栓拧紧设备的缺陷
车辆总装配过程中螺栓的拧紧除骑马螺栓和轮胎螺栓是采用专用的定扭拧紧设备来操作外, 其余的螺栓主要靠气动扳手来拧紧, 而普通的气动扳手无法实现定扭功能, 螺栓锁紧之后的扭矩大小无法得到精确的控制, 导致螺栓扭矩出现偏差。
二、车辆生产过程中出现的扭矩偏差问题及理论分析
这些问题有:
1)半浮式驾驶室后悬部位的螺栓扭矩偏差反复较明显。
分析:驾驶室半浮式后悬, 由于增加了减震弹簧, 导致其宽度增加, 根据其结构特点 (U型结构, 螺栓安装孔在U型结构的底部) , 宽度增加后其与纵梁腹面配合的安装孔位置偏靠内, 空间局限, 气动扳手无法按常规方式 (驱动头+套筒) 对该处螺栓进行锁紧;需配合转接杆和万向套筒对该处的螺栓进行紧固, 而接杆的形变和万向套筒的甩动会造成其扭矩不易控制。
2)尿素箱支架和膨胀水箱支架等的紧固螺栓扭矩偏低。
分析:上述支架为方管空心结构, 实施紧固后, 螺母与方管的接触面发生塑性形变, 螺栓锁紧到规定扭矩将导致支架塑性形变过大, 为避免装配后支架塑性形变过大而导致该处扭矩无法达到标准值范围。
3)轻卡驾驶室后悬紧固螺栓扭矩偏差。
分析:轻卡车型的车架为单层梁和变截面结构, 其强度小于双层梁车架, 造成车架的承载变形和误差在驾驶室后悬处的钟摆放大效应更加明显, 驾驶室后悬支座出现不同程度的横向位移, 位移量超出锁止机构的预留量。为消除这种位移而在驾驶室后悬与车架纵梁腹面间临时增加调整垫片;因该处为4点紧固方式, 而调整垫片只垫于其中的上面2点, 形成后悬安装面与纵梁腹面上下不等距的情况, 4点紧固的翘板效应因此而放大, 若按常规的交叉递进锁紧方式, 易造成螺栓扭矩的跳跃分布。
4)车辆下线后骑马螺栓扭矩出现阶段性的扭矩衰减。
分析:板簧安装形式的特殊性和结构的差异性——在车架翻转前其承载对应车桥的重量、在车架翻转后其簧上质量随着零部件的装配过程而不断变大直到车辆下线达到一个相对固定值、在车辆装厢后其簧上质量达到车辆出厂时的最大状态, 这3个过程板簧受到的力和形变量均变大, 作用在骑马螺栓力逐渐减小。根据螺栓的扭矩原理, 螺纹副间的相互作用力减小, 螺纹副间的摩擦力因此减小;同时由于螺母与其支撑面的作用力减小, 造成螺母与支撑面的摩擦力也相应变小, 因而骑马螺栓扭矩值呈下降趋势。
对于正向安装的钢板弹簧, 钢板弹簧凹曲方向与骑马螺栓的拧紧方向相反, 因此通过对骑马螺栓的拧紧可以实现钢板弹簧的安装。拧紧后的钢板弹簧如图1所示, 此时钢板弹簧骑马螺栓弧高由ε减小到ε′。根据理论分析, 板簧基本可以实现ε≈0, 即骑马螺栓距内部分的钢板弹簧压平, 钢板弹簧紧固到理想状态。
图1 骑马螺栓受力图
骑马螺栓的受力状态为:F= (F1+F2) /4, 其中F1为骑马螺栓工作载荷、F2为克服骑马螺栓距内钢板弹簧变形的力。因骑马螺栓受力大小变化, 导致骑马螺栓在不同阶段其扭矩衰减量也不同。
5)平衡悬架支座螺栓扭矩出现下降。
分析:平衡悬架支座与纵梁腹面的配合螺栓, 由于其公称直径为20 mm, 其扭矩要求值在现有的 (1/2) ″气动扳手的最大扭矩值区间;气动扳手长期在极限扭矩下使用, 其内部零件金属疲劳和异常磨损, 最终导致其性能下降, 有效输出值降低。
6)涂抹螺纹紧固剂的螺栓未达到预期的扭矩。
分析:螺纹锁固剂涂抹量不够或过早涂抹螺纹锁固剂导致螺纹锁固剂流失, 造成螺纹锁固剂未填满整个螺纹副间隙部分, 紧固剂实际的防松能力下降。采取螺纹锁固剂的螺栓后期 (紧固剂完全固化后) 有拆卸或调整, 螺纹锁固剂凝固层被破坏后并未重新涂抹螺纹锁固剂, 造成螺纹锁固剂效果下降。
7)零部件的法兰带齿螺栓扭矩防松能力下降。
分析:紧固部位的法兰锁止齿凹槽被零部件表面过厚的漆膜填满 (螺栓在锁紧的过程中锁止齿将破坏漆膜) , 法兰锁止齿嵌入量有限;根据螺栓扭矩原理, 螺栓与支撑面的摩擦力变小, 无法达到预期紧固效果。
三、实际生产验证
针对上述出现的螺栓扭矩偏差问题, 通过实际试验收集数据分析和实际生产验证, 进行整改后, 扭矩控制效果良好。分述如下:
1)半浮式驾驶室后悬横向方向的紧固螺栓采用气动扳手加转接杆和万向套筒的方式进行紧固, 锁紧时弱手辅助握紧转接杆减少因为使用万向套筒造成的甩动, 同时采用预置式扭矩扳手对该位置螺栓进行复紧, 扭矩偏差反复明显的现象得到改善。
2)对于方管结构的零部件, 采用增加螺纹紧固剂的方式弥补不足的扭矩部分, 扭矩达到要求的同时方管却无凹陷。
通过试验数据验证螺纹紧固剂可以作为螺栓扭矩的一种补偿措施。采取4种配合方式验证不同强度螺纹锁固剂的锁固效果, 实验数据采取正向拧紧和反向拆卸的方式获取, 如表1所示。
3)对于采用增加调整垫片的驾驶室后悬, 取消交叉递进的锁紧方式, 采用同侧单边递进锁紧后复锁先前螺栓的方式, 轻卡驾驶室后悬螺栓扭矩值跳跃分布的情况得到改善。
4)骑马螺栓扭矩值收集及数据分析, 具体分析解决过程如下:
测量连续生产的40辆份整车的骑马螺栓扭矩值 (偏差比例见表2, 骑马螺栓位置见图2) , 其值在空载及加载后均比整车装配时要偏低20%~50%。 (注:福建海西汽车有限公司生产的工程型自卸车分为底盘车和装厢车2种状态, 底盘车为空载, 装厢车为加载)
图2 各个位置的骑马螺栓
表1 螺螺栓栓紧紧固固胶胶性性能能验验证证记记录录 (30 h数据数据)
注:1) 正向破坏扭矩指正常测螺栓扭矩所得的值。2) 实验结果:相对于无涂胶情况, 螺栓涂271高强度胶时, 拧紧时存在6%~35%的附加扭矩, 拆卸时存在22%~61%的附加扭矩;螺栓涂242中强度胶, 拧紧时存在16%~87%的附加扭矩, 拆卸时存在21%~46%的附加扭矩。
表2 骑马螺栓扭矩偏差比例
(1)分析对比前桥骑马螺栓翻转时与整车空载的扭矩数据 (见表3) , 得出车辆空载行驶后, 前桥8处螺栓的扭矩衰减均值线性平衡率:
线性平衡率较高, 可判断前桥8处骑马螺栓的扭矩衰减量基本稳定, 可将各处衰减量均值作为装配过程扭矩标准的补偿量, 即车辆空载时前桥骑马扣扭矩补偿量=sum (A, B, C, D, E, F, G, H) /8=83 N·m。为便于操作前桥M18骑马螺栓, 取扭矩补偿量为80 N·m, 根据拧紧时扭矩设定值为380 N·m, 得出空载时前桥骑马螺栓扭矩衰减补偿量为设定值的21%。
(2)分析对比前桥骑马螺栓翻转时与整车加载后的扭矩数据 (见表4所示) , 得出车辆加载行驶后, 前桥8处螺栓的扭矩衰减均值线性平衡率:
表3 前桥骑马螺栓翻转时与整车空载的扭矩数据
表4 前桥骑马螺栓翻转时与整车加载后的扭矩数据
线性平衡率较高, 可判断前桥8处骑马螺栓的扭矩衰减量基本稳定, 可将各处衰减量均值作为装配过程扭矩标准的补偿量, 即车辆加载时前桥骑马扣扭矩补偿量=sum (A, B, C, D, E, F, G, H) /8=117 N·m。为便于操作取前桥M18骑马螺栓, 扭矩补偿量为120 N·m, 根据拧紧时扭矩设定值为380 N·m, 得出加载时前桥骑马螺栓扭矩衰减补偿量为设定值的31%。
为了便于计算, 前桥骑马螺栓统一取底盘车 (空载) 时, 扭矩补偿量为设定值的20%;装厢车 (加载) 时, 扭矩补偿量为设定值的30%。补偿量汇总如表5所示。
(3)分析对比后桥骑马螺栓翻转时与整车空载的扭矩数据 (见表6) , 得出车辆空载行驶后, 后桥8处螺栓的扭矩衰减均值线性平衡率:
线性平衡率较高, 可判断后桥8处骑马螺栓的扭矩衰减量基本稳定, 可将各处衰减量均值作为装配过程扭矩标准的补偿量, 即车辆空载后桥骑马扣扭矩补偿量=sum (A, B, C, D, E, F, G, H) /8=86 N·m。为便于操作取后桥M20骑马螺栓, 扭矩补偿量为90 N·m, 根据拧紧时扭矩设定值为480 N·m, 得出车辆空载后桥骑马螺栓扭矩衰减补偿量为设定值的19%。
(4)分析对比后桥骑马螺栓翻转时与整车加载后的扭矩数据 (见表7) , 得出车辆载重 (装厢) 后, 后桥8处螺栓的扭矩衰减均值线性平衡率:
表5 自卸车型前桥骑马螺栓扭力衰减补偿量汇总
表6 后桥骑马螺栓翻转时与整车空载的扭矩数据
表7 后桥骑马螺栓翻转时与整车加载后的扭矩数据
线性平衡率较高, 可判断后桥8处骑马螺栓的扭矩衰减量基本稳定, 可将各处衰减量均值作为装配过程扭矩标准的补偿量, 即车辆载重 (装厢) 后桥骑马扣扭矩补偿量=sum (A, B, C, D, E, F, G, H) /8=136 N·m。为便于操作取后桥M20骑马螺栓, 扭矩补偿量为140 N·m, 根据拧紧时扭矩设定值为480 N·m, 得出车辆载重 (装厢) 后桥骑马螺栓扭矩衰减补偿量为设定值的29%。
为了便于计算, 后桥骑马螺栓统一取底盘车 (空载) 时, 扭矩补偿量为设定值的20%;装厢车 (加载) 时, 扭矩补偿量为设定值的30%。补偿量汇总如表8所示。
根据骑马螺栓扭矩测量数据分析结果, 对骑马螺栓扭矩控制进行优化:车架翻转前骑马螺栓拧紧时拧紧机设定值为工艺要求的上限+扭矩衰减补偿量。对骑马螺栓增加扭矩补偿方式后, 骑马螺栓的扭矩测量数据如表9所示;对比表2, 扭矩控制得到了改善。
5)更换平衡悬架工位的气动扳手为 (3/4) ″型号, 其理论最大工作扭矩800 N·m, 可避免气动扳手长期在极限扭矩下使用而失效, 确保气动扳手输出扭矩值的有效性。
6)涂抹螺纹紧固剂的螺栓按正确方式 (足量准时补涂) 操作后, 其扭矩值达到预期。
7)配件厂对螺栓作用处的漆膜偏厚问题进行整改后, 法兰带齿螺栓的防松效果得到改善。
四、结论
通过上述分析改进验证, 改善不同部位螺栓扭矩控制方法, 能有效杜绝其扭矩偏差反复的现象, 使整车扭矩控制方式趋向合理性, 减少了扭矩失效的隐患。经验总结如下:
1)针对紧固部位的操作空间偏小而采取万向套筒的情况, 可采取预置式扭矩扳手复紧螺栓作为螺栓扭矩不足的补偿措施。
2)针对紧固部位的材质为非实心结构 (比如方管) , 可采取螺栓涂抹螺纹紧固剂的方式作为螺栓扭矩的补偿措施。
3)紧固部位的安装孔呈矩形四顶点分布, 但配合面非零间距, 常规的交叉递进锁紧方式存在缺陷;这种情况下应采用同侧单边递进锁紧后复锁先前螺栓的方式。
4)紧固部位的结构为弹性部件, 受到变化的载荷后发生形变, 导致在螺栓锁紧到规定扭矩的前提下, 车辆入库前仍会出现扭矩衰减;这种情况需要螺栓拧紧时在规定扭矩的基础上增加一个扭矩衰减补偿量。
表8 自卸车型后桥骑马螺栓扭力衰减补偿量汇总
表9 骑马螺栓扭矩补偿后测量结果
5)紧固部位的气动扳手型号偏小, 长期使用最大挡, 造成气动扳手性能下降;应采取增大气动扳手型号的措施, 使气动扳手输出扭矩的中间值在螺栓的规定扭矩范围。
6)螺栓涂抹螺纹紧固剂要严格按照紧固剂的使用规范, 确保足量准时及螺栓调整后的补涂, 这样才能发挥螺纹紧固剂的作用。
7)螺栓防松效果下降, 需关注螺栓紧固处的漆膜太厚的情况, 避免因漆膜厚度偏大造成螺栓与零部件接触面摩擦力下降, 导致法兰带齿螺栓的防松效果下降。
福利:做任何事情,都有方法。比如汽车行业如何最短时间内获取高薪,其实,是一件很容易的事情,结合汽车行业十多年工作经历,我做了一次系统全面总结无偿分享大家,文章共计十篇。帮助更多的网友在汽车行业快速发展。同时,我业余时间整理一套免费经典的CATIA视频教程, 汽车设计领域必备软件工具,大家有需要的,可以给我留言,请加qq:1011852705,微信qifei1799。提“启飞”就可以获取下载链接:汽车行业快速突破月薪过万绝密分享和catia视频精品一套。明确方向,精准学习,为以后在汽车行业职场做好铺垫。
CONTATC
重庆市渝中区中华路1号LG层LG13号81#
15923339397
2248511017
qifei1899
微信二维码
Copyright © 2002-2018 重庆启飞汽车设计有限公司版权所有渝ICP备18000729号 电话:15923339397