启飞汽车
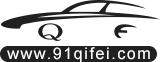
启飞汽车设计汽车设计— 国内专业产品设计培训基地!咨询热线:+86-15923339397
为中小型企业汽车研发和制造提供解决方案
专业承接整车设计开发项目
为各大主机厂,高校提供专业专项培训
为设计爱好者、毕业生提供专业系统培训
2019-02-12121作者:启飞汽车设计
摘要
近年来汽车工业发展迅速, 新车上市速度越来越频繁, 高强钢在汽车冲压件中的应用变得更加广泛。对比了2种汽车冲压件简化模型, 提出了U形简化模型的合理性。结合生产实际, 构建出了1个U形汽车冲压件简化模型。根据该模型选取热冲压高强钢22MnB5作为冲压材料, 进行计算模拟, 验证了这个U形汽车冲压件简化模型的可行性。研究表明:采用U形汽车冲压件简化模型科学合理, 构建出的U形汽车冲压件简化模型符合需求, 可用于指导实际汽车冲压件生产。
一、模型简化
在60年代, 随着板材成形技术的发展, 成形极限图 (FLD) 的提出推动了板材性能、成形理论、成形工艺和质量控制的协调发展, 成为板材成形技术发展史上的一个里程碑。其试验方法如下:在试验用坯料上制备好坐标网格;以一定的加载方式使坯料产生胀形变形, 测出试件破裂或失稳时的应变ε1、ε2 (长、短轴方向) ;改变坯料尺寸或加载条件, 重复试验, 测得另一状态下的ε1、ε2;取得一定量的数值后, 在平面坐标图上描绘出各试验点, 然后圆滑连线, 作出FLD。成形极限曲线将整个图形分成如图1所示的三部分, 即安全区、破裂区及临界区。
图1 实验成形极限图
然而, 在大型汽车薄板零件冲压过程中, 由于在奥氏体区变形, 变形温度较高。采用成形极限图方法难以保持某一固定的高温, 对于高温变形过程, 成形极限图方法变得难以实现。随着三维建模和数值模拟技术的发展, 更好的解决办法开始出现。用数值模拟还可以实现对耦合场的分析, 针对薄板计算模型来说, 可以准确预测破裂或者失稳的区域, 检测钢铁材料在相关冲压变形过程中的成型性能。
目前来看, 大型汽车支撑类的冲压件主要有保险杠和支撑柱 (A、B、C) 、防撞梁等, 如图2所示, 通过观察, 发现支撑结构件主要呈现出中空的凹形, 如图3所示。
图2 车身结构
图3 保险杠
根据支撑结构件的形状特点, 目前主要有2种简化模型, 一类是矩形盒模型, 另一类是U形模型。对于矩形盒模型来说, 重点观察研究的是法兰边的减薄和起皱。对于U形模型来说, 则主要观察研究的是开裂、回弹和工艺优化。对于现代汽车制造形式来看, 汽车支撑构件逐渐呈现流线形的设计, 力图避免小的矩形盒类的形状出现, 这也是符合生产过程中提高产品合格率的要求, U形模型方案被采用的频率开始加快。目前越来越多的人开始针对U形模型进行研究, 形成了汽车汽车支撑结构件冲压模型研究的主流趋势。
二、U形汽车冲压件简化模型的设计
需要构建的U形零件简化模型如图4所示, 这是专门针对凹形截面简化设计的。综合以往广大研究者来看, 其中凹槽的深度主要取值范围是40~60mm之间。为了更好地检测材料性能, 采用深度较大的设计数值57.91mm。
图4 U形汽车冲压件简化模型
汽车支撑件的厚度 (即冲压坯料厚度) t一般位于1.0mm到2.5mm之间, 由于小于3mm, 凹模圆角半径r凹的取值
为了适应大范围汽车冲压件材料冲压质量的检测, 选取圆角半径r凹为13mm, 其适用的板料厚度可达1.3~2.16mm, 特别符合实际的大部分冲压材料厚度。冲压过程凸模的圆角半径要略小于底部零件的圆角半径, 凸模的圆角半径r凹和凹模的圆角半径r凹共同决定了模具间隙g的大小, 用公式 (2) 表示如下。
汽车板热冲压过程中通常要考虑淬火, 通常需要模具中的冷却水带走热量, 凹模的成本会比凸模的成本高一些。采用1个圆角半径r凹为13mm的凹模和不同圆角半径的凸模来针对不同厚度 (1.3~2.16mm) 的冲压坯料进行冲压测试会更加经济划算, 故再确定多个凸模 (圆角半径不同) 来形成最终的U形汽车冲压件简化模型。考虑到模内淬火, 模具间隙不能太大, 否则会增大和空气间的接触, 影响到模具淬火效果, 模具间隙与坯料的厚度关系如下:
将公式 (3) 代入公式 (2) 中, 可得到凸模圆角半径r和坯料厚度的关系:
r凹值为13mm, t的取值范围为1.3~2.16mm, 由公式 (4) 所得到r凸的取值范围为10.624~12.7mm。为了尽量减少凸模的数量, 辩证考虑凸模圆角半径的规范化、满足不同坯料厚度的模具间隙适用性和更换不同厚度冲压坯料试验的方便性, 归纳整理U形汽车冲压件简化模型的凸模圆角半径、模具间隙、适用的坯料厚度关系如表1所示。
表1 不同凸模圆角半径下的模具间隙和坯料厚度范围/mm
三、热冲压过程模拟验证
由于变形过程的对称性, 为了简便计算, 采用冲压过程的1/4模型部分进行模拟运算。利用三维软件Creo制作的1/4几何冲压模型如图5所示。
图5 1/4几何冲压模型
使用DEFORM软件, 选用热冲压材料22MnB5对U形汽车冲压件简化模型进行冲压过程数值模拟。选取板料厚为1.41mm, 根据表1判断凸模圆角半径为11.5mm, 度板料开始冲压的初始温度为900℃, 模具温度为20℃, 冲压速度为50 mm/s。设定板料与模具之间的摩擦系数为0.1, 传热系数为50N/s/mm/℃。
获得冲压材料在不同冲程下的温度场如图6所示, 在不同冲程下的应力场如图7所示。
图6 不同冲程下的温度场
图7 不同冲程下的应力场
通过图6可以看出, 随着变形过程的进行钢板温度逐渐降低, 变形结束时 (Step 500) 的低温区域温度在600℃以上, 高于马氏体开始转变温度 (385℃) , 变形过程中没有发生相变, 为接下来模内淬火提供了良好的奥氏体环境。通过图7可以看出, 凸模、凹模圆角附近应力值始终比较大, 同时由于温度场分布不均及板料与模具接触为曲面接触, 导致板料的应力场分布不均;可以看出, 随着变形过程的进行钢板应力逐渐增大, 变形结束时 (Step 500) 的应力较大区域应力值在500 MPa左右, 这时也是材料冲压测试中容易发生材料破坏的时间。
通过有限元模拟, 展示了U形汽车冲压件简化模型在冲压过程中的变形规律、温度场分布和应力场分布, 验证了模型的理论可行性, 为实际的材料冲压测试提供了可靠的理论基础。
四、结论
(1)结合汽车支撑结构材料冲压件构建了冲压深度为57.91mm的U形汽车冲压件简化模型, 采用与之对应的1个圆角半径为13mm的凹模和8个不同圆角半径的凸模构成研究高强钢材料冲压成形性能的模型组, 可用于研究的坯料厚度为1.3mm到2.16mm, 符合目前汽车生产制造的需求。
(2)通过有限元模拟, 展示了U形汽车冲压件简化模型冲压过程中的变形规律、温度场分布和应力场分布, 验证了模型的理论可行性, 为实际的材料冲压测试提供了可靠的理论基础。
作者:刘全义 张贵杰 来源:华北理工大学学报
福利:做任何事情,都有方法。比如汽车行业如何最短时间内获取高薪,其实,是一件很容易的事情,结合汽车行业十多年工作经历,我做了一次系统全面总结无偿分享大家,文章共计十篇。帮助更多的网友在汽车行业快速发展。同时,我业余时间整理一套免费经典的CATIA视频教程, 汽车设计领域必备软件工具,大家有需要的,可以给我留言,请加微信qifei1799。提“启飞”就可以获取下载链接:汽车行业快速突破月薪过万绝密分享和catia视频精品一套。明确方向,精准学习,为以后在汽车行业职场做好铺垫。
CONTATC
重庆市渝中区中华路1号LG层LG13号81#
15923339397
2248511017
qifei1899
微信二维码
Copyright © 2002-2018 重庆启飞汽车设计有限公司版权所有渝ICP备18000729号 电话:15923339397