启飞汽车
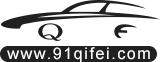
启飞汽车设计汽车设计— 国内专业产品设计培训基地!咨询热线:+86-15923339397
为中小型企业汽车研发和制造提供解决方案
专业承接整车设计开发项目
为各大主机厂,高校提供专业专项培训
为设计爱好者、毕业生提供专业系统培训
2018-08-2250作者:启飞汽车设计
摘要
通过分析精益生产的衡量指标及价值创造理论, 研究了汽车整车装配工艺精益性开发的标准。结合汽车公司在产品开发阶段及试生产过程中总装工艺规划存在的一些实际问题及详细解决方案, 提出将总装工艺精益性开发标准贯穿于产品开发及批量生产前的各个阶段, 从源头上减少批量生产中的浪费现象, 实现总装车间基于价值导向的精益生产模式。该方法对汽车企业的总装工艺规划具有一定的参考价值和实际可操作性。
一、精益生产规划的衡量指标及操作准则
1.精益生产规划的衡量指标
哈勃工时 (Hours Per Vehicle, HPV) 即单车消耗工时, 它是指一定时期内生产的车辆平均消耗的出勤工时。HPV=所有从事批量生产人员的实际工时/总产量。通过HPV, 可以看到公司在人员上的总费用。
HPV由美国哈勃咨询公司提出, 它的创始人Jim Harbour曾经担任美国克莱斯勒公司产品制造主管。从1989年开始, 哈勃公司每年发布一份汽车行业报告, 主要内容是在研究冲压、整车制造、发动机和变速箱工厂的基础上, 根据各厂商生产一辆汽车所需要的时间来衡量其各生产环节效率的高低。自1991年起, HPV被视为汽车领域常用的绩效考核指标, 是很多汽车厂商和供应商衡量业绩、调整发展策略以及改善经营手段的依据。
HPV的组成部分如图1所示, 其中, 制造工时是其核心内容;因此, 基于精益生产的总装工艺规划的工作重点主要体现在制造工时的优化, 即降低产品决定的制造工时及过程决定的制造工时。
图1 HPV组成部分
按照价值创造理论, 可以把总装制造工时分为3个部分:产生增值的工作、隐含浪费的工作及明显的浪费 (见图2) 。
图2 总装制造工时分类
对于明显的浪费, 即对产品增值明显不必要的外围工作, 例如返修、零件拆包装, 目标是完全消除;对于隐含的浪费, 即不会带来增值, 但是在既定条件下必须要做的边缘工作, 例如, 零件运输、工具操作、零件放置和取料路线等, 目标是降到最低;对于增值的工作, 即使产品增值的核心工作, 客户愿意付费的工作, 例如, 拧螺钉、装配、加液和产品要求的检测工作等, 目标是提高比例。
2.精益生产规划的操作准则
为了更好地帮助员工理解总装精益规划的理念, 从而实现以创造价值为导向的精益化混线生产规划, 在精益化总装工艺规划过程中, 需要建立一定的准则, 使其更具操作性。基于精益生产规划的操作准则包括减少浪费、集中在工作区域的工作、一触一动、生产线平衡创造价值、考虑人机工程学。
2.1减少浪费
总装工艺流程的每一个工序都包含创造价值和浪费两部分, 而减少浪费在工艺流程中直观表现为制造工时的减少, 由此降低HPV。可见, 减少浪费的准则也是精益生产规划的核心部分。减少浪费包括如下几方面。
1)等待。在人或机器的工作过程, 或在其活动的封闭环境中, 会存在相互等待时间, 包括人等人、人等机器。例如, 等待前道工序的完成, 等待维修或设备安装调试和停工待料等。
2)不必要的移动/动作。工艺过程中由人员/机器提取部件/工具/资料均为耗费, 应予排除或压缩到最低限度。例如, 零部件或工具不在工人能触及到的20~50cm内, 导致其取料或工具行走距离过长, 工人动作过多等。
3)不必要的过程。包括重复作业、多次检查、返修和拆除零件包装等。
4)缺陷/返工。缺陷/返工造成的浪费即意味着增加费用、等待时间。其使成本提高, 令客户失望。
2.2集中在工作区域的工作
整车总装的工作区域一般可分为5个部分:前盖、后盖、车身左侧、车身右侧及车内。在同一个装配工位上, 工人应在各自的工作区域内进行零件装配, 无互相干涉的操作。每个工人理想的工作区域数量为1, 这样有利于减少不必要的走动。
工作区域的理想划分:前后2个相邻节拍不安排同一工作区域的零件安装。这样做的好处在于, 如果前一个工位出现故障不能在一个节拍内完成工艺内容, 不会影响到后一工位的工艺内容。理想的总装流水线工作区域安排如图3所示。
图3 理想的总装流水线工作区域安排
在同一工位上出现2名工人的情况下, 应尽量将他们的工艺内容安排在不同的工作区域, 避免装配过程中的互相碰撞和干涉。
如果1名工人的工艺内容包含数个工作区域, 其零件安装顺序应与流水线方向相反, 以减少不必要的走动 (见图4) 。
图4 单人多个工作区域的零件装配顺序
2.3一触一动
“一触一动”的准则在零件设计上体现为:1) 首次装配后即无需抓住;2) 无需后续定位和再次用力;3) 零件造型适合一人手工操作;4) 1名工人可以在1个节拍内使用1个工具完成此零件装配;5) 零件自身带定位, 无需调整;6) 零件装配无需使用辅助工具定位。
在工艺流程上体现为:1) 工人直接拿起并装配零件;2) 在拿起和装配过程中间无需再更改位置;3) 零件在不能自行定位情况下, 工具应带有辅助定位功能, 无需另加工具。
2.4生产线平衡及创造价值
生产线平衡是指生产过程中按照正确的装配顺序对工序进行调整;在既定的节拍时间内优化每个工位的劳动负荷率。创造价值是指通过人工、机械化或自动化工作/方法提升产品价值的行动。每个工人的劳动负荷率=工艺时间/节拍时间。
对于一条稳定的生产线, 节拍时间是固定的, 即每个工人在每辆车能够装配的时间是固定的。工艺时间是指工人根据工艺流程完成该工位安排的工序所需的时间, 即工人在每辆车花费的实际装配时间。
该标准的目标在于:1) 生产线上所有车型在工位上的劳动负荷率达到最大的100%;2) 将同一工位上不同车型或同一车型高低配之间的工时不平衡现象降到最小;3) 在工艺流程中减少浪费, 增加增值部分的工作。
生产线平衡及创造价值是总装精益生产规划开展过程中非常基本和重要的准则。其操作步骤如下:1) 按照零件的装配顺序说明各工位的工艺内容;2) 按照增值部分和非增值部分分析车辆装配的每一道工序;3) 使用各类操作准则减少非增值部分;4) 根据优化后的工艺内容及工时, 进行工位之间的节拍调整, 将柔性工序拆分安排到固定工序, 目的是尽可能减少工位上不同车型之间的工时不平衡现象 (柔性工序是无设备限制和装配顺序限制的工艺流程;固定工序是根据零件的装配顺序或者设备限制必须在特定工位完成的工艺流程, 例如, 需使用机械手安装的零件、加液、底盘合装等) 。
2.5考虑人机工程学
人机工程是借助于工作系统的有效机构, 在尊重人的工作效率和需求的同时, 创造人、设备和工作对象的最佳协同作用。其目的如下:1) 建立人性化的工作场地和流程;2) 避免员工超负荷工作;3) 通过人体工程学的工位设计提高负荷率。
符合人机工程的工艺流程应避免如下现象:1) 不自然的体姿, 例如, 长期弯腰的体姿、高于身体的作业和强制体姿等;2) 复杂的身体动作, 例如, 进出车身、弯腰、弯曲、拉伸和扭转等;3) 过大的用力, 例如, 需用力安装闷盖/卡扣等;4) 高负载作业, 例如, 负载行走;5) 符合人机工程学的装配允许工人的站立作业高度在膝盖和肩膀之间, 必要时应提供座椅。
人机工程学标准在产品设计和工艺流程规划期间都应予以考虑, 并且在零件的实车模拟中进行评估。
二、基于精益生产的总装工艺规划
基于精益生产的总装工艺规划贯穿于产品开发至批量生产前的各个阶段, 通过不同的工作重点体现。产品开发阶段主要体现在如何降低产品设计决定的制造工时, 即由产品 (零件) 设计决定生产一件产品所需的时间, 只有通过改变产品的设计才能缩短时间, 不受产地、产量和自动化程度的影响;对于产品数据冻结至批量生产之前, 体现在降低过程决定的制造工时具体指工艺流程中的非增值时间。通过不同形式的精益生产规划, 最终获得最优的制造成本。
1.产品设计同步工艺规划
总装工艺规划以同步工程的形式介入产品开发阶段, 对生产系统进行同步开发, 产品与工艺、工装的开发同步规划, 使开发者从概念开始就考虑生产系统的需求, 考虑产品后续的工艺性。通过在开发初期进行先期工艺评价和验证, 将生产过程中可能出现的问题尽可能地在造型阶段和结构设计初期发现并解决, 从而避免之后需要投入大量的人力成本解决由于零件设计导致的装配问题, 使投产更可靠和精益化, 同时降低装配成本。
这一阶段的特点是以虚拟数据及模型为载体, 进行零件的工艺流程分析, 工作重点主要集中在如下几点:1) 降低由于产品设计所影响到的生产时间;2) 考虑混线车型的零件特点, 通过对零件的标准化设计, 保证工艺流程的标准化和稳定性;3) 确定零件的装配顺序;4) 设计符合人机工程学的生产工艺;5) 提高产品质量;6) 降低原料成本。
案例1:对某车型轮罩的工艺分析, 该车型规划在60JPH车间生产。优化前、后轮罩固定方式如图5所示。
图5 轮罩固定方式
优化前, 轮罩无法预先固定于车身。虽然轮罩边缘可以挂在车身上, 但是不能确保其不掉下来。需要2名工人才能完成固定装配, 而且工人1需要双手操作, 并且需要1辆随行小车, 保证工人1在一只手定位轮罩的情况下, 另一只手可以从小车上够取螺栓和充电枪进行紧固。优化后, 轮罩可以通过卡扣固定于车身, 无需用手定位。其优点体现在:1) 更好地实现了直接抓取并安装零件;2) 更容易定位;3) 节约1辆随行小车;4) 降低工时及人员成本。
轮罩固定方式优化分析见表1。
表1 轮罩固定方式优化分析
通过更改零件设计, 降低产品决定的制造工时, 并优化工艺流程, 是在产品设计阶段进行精益化工艺规划的典型案例。
2.为生产准备的工艺规划
这一阶段的工艺规划, 通常以实车演练作为载体, 推行工艺规划的“规划→模拟→优化”操作, 主要包括如下4个环节。
1)模拟装配流程。使用零件及工具, 根据工艺规划方案进行实物装配, 并对整个流程 (1个岗位单节拍的工作内容) 进行摄像。
2)IE (Industry Engineer) 工程师进行工时分析。根据录像中详细的零件装配过程, 将工艺流程分解成动作要素, 进行MTM (Methods-Time Measurement) 分析, 创建每个零件的工时模块及价值分类, 得到每个工人的工时及劳动负荷率。
3)小组成员讨论。利用各类精益生产标准, 评估工艺流程, 并对问题进行分类, 提出解决问题方案。目标是减少浪费, 优化工艺流程。
4)模拟最优装配流程并拍摄视频, 用于培训批量生产操作工。
在开展为生产准备的工艺流程过程中, 通过实物拆装模拟和流水线现场巡视, 进行设备、工艺流程、工位布置、工时平衡、以及物料包装及上线方案等的精益规划。对产品设计阶段同步建立的工艺规划方案进行验证及细化, 规避潜在的风险, 实现以创造价值为导向的精益化生产方式, 改善混线生产的工时不平衡现象;同时提高混线车型起步生产阶段的工艺稳定性, 缩短起步生产时间, 提高起步生产及批量生产之后车辆的装配质量。
为生产准备的工艺规划阶段, 其主要工作内容有如下几点:1) 在实车上对每一道工序进行实际操作的模拟;2) 优化并确定以MTM为基础的精益化工艺生产流程;3) 设计工装器具;4) 改善工位布置及人机工程;5) 降低混线生产车型之间的工时差异;6) 定义所有零件的上线方式、位置及零件包装方式。
案例2:通过对制动液加注、踏板力测试、雨刮安装工艺的调整, 减少非增值时间, 优化人员。工艺优化前、后3名工人的制造工时如图6所示, 图6中工时分类与图2相同。工艺调整分析见表2。
图6 工艺优化前、后的制造工时图
表2 工艺调整分析
根据制造工时的价值理论分类及精益生产规划的标准, 优化之前工艺存在的问题如下:1) 插接电源, 开起点火开关分别是制动液加注和雨刮零位调整的准备工作, 工人1和工人3操作重复;2) 工人2在进行踏板力测试时, 存在等待设备的时间, 属于明显的浪费。
根据上述分析, 雨刮零位调整作为柔性工艺, 可以由工人1操作, 从而避免了插接电源, 开起点火开关在整体工艺流程中的二次操作, 减少了非增值时间;工人2可以利用等待踏板力测试的时间, 进行雨刮安装工作, 从而消除浪费。
通过上述工艺调整, 降低了非增值时间, 原本需要3名工人完成的总装装配及检测工作可由2名工人完成, 实现了总装工艺的精益规划, 降低了HPV。
3.起步生产阶段工艺验证及优化
在新产品批量生产之前的试生产阶段, 需要在生产现场验证之前的工艺规划并做进一步的精益性优化。在试生产前期, 要求流水线严格按照新产品混线工艺进行生产, 在此过程中, 评价工艺流程与流水线现场的匹配程度, 通过对每个岗位的现场观察发现问题。每一个问题都是改进的机会, 针对每一个装配流程问题的解决方案, 就是对工艺流程的精益优化。
起步生产阶段工艺验证及优化的主要工作内容如下:1) 结合现场情况进行工艺流程确认, 并对问题提出解决方案;2) 检查流水线设备位置、操作方式及设备时间是否和为生产准备的工艺规划一致, 如不一致, 需要调整工艺;3) 汇总所有的产品更改信息, 并在此基础上调整工艺计划;4) 检查工装器具并根据现场使用情况进行优化;5) 检查每个工位的物流上线方式及包装形式并根据现场情况进行优化。
案例3:根据现场实际生产问题, 制作特殊工具, 优化工时, 降低费用。工艺优化之前使用胶带固定线束, 存在工时和材料费用的双重浪费, 而且胶带的使用是伴随车辆生命周期的长期投入。优化之后使用夹头固定, 不仅降低了制造工时, 而且由于夹头是一次性投资, 平均到每台车的费用几乎可以忽略不计。优化前、后线束固定方式如图7所示。具体工时及费用优化见表3。
图7 优化前、后线束固定方式
表3 线束固定方式优化工时费用分析
三、总结
综上所述, 基于精益生产的汽车总装工艺规划是一个系统性的工程, 它贯穿于产品开发至批量生产前的各个阶段。在进行工艺的精益规划之前, 应掌握精益生产的操作准则, 才能对总装工艺的精益性进行有效的评估。本文所介绍的方法都已在实际的项目中运用, 期望随着更多项目的开展, 可以积累详实的数据和经验, 促进汽车总装工艺的精益化及标准化发展。
福利:做任何事情,都有方法。比如汽车行业如何最短时间内获取高薪,其实,是一件很容易的事情,结合汽车行业十多年工作经历,我做了一次系统全面总结无偿分享大家,文章共计十篇。帮助更多的网友在汽车行业快速发展。同时,我业余时间整理一套免费经典的CATIA视频教程, 汽车设计领域必备软件工具,大家有需要的,可以给我留言,请加qq:1011852705,微信qifei1799。提“启飞”就可以获取下载链接:汽车行业快速突破月薪过万绝密分享和catia视频精品一套。明确方向,精准学习,为以后在汽车行业职场做好铺垫。
CONTATC
重庆市渝中区中华路1号LG层LG13号81#
15923339397
2248511017
qifei1899
微信二维码
Copyright © 2002-2018 重庆启飞汽车设计有限公司版权所有渝ICP备18000729号 电话:15923339397