启飞汽车
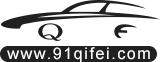
启飞汽车设计汽车设计— 国内专业产品设计培训基地!咨询热线:+86-15923339397
为中小型企业汽车研发和制造提供解决方案
专业承接整车设计开发项目
为各大主机厂,高校提供专业专项培训
为设计爱好者、毕业生提供专业系统培训
2017-08-26168作者:启飞汽车设计
摘要:汽车制造企业的车间布局是生产系统设计与优化的重要内容,它的优劣直接影响汽车制造的效率和企业的经济效益。本文运用系统布置设计方法,通过对某汽车制造企业总装车间的工艺流程分析以及作业单元划分,明确各作业单位间的物流与非物流关系,得到各作业单元之间的综合相关性。然后,运用加权因素比较法对车间布局优化方案进行评价,评价结果显示优化方案能够改善车间布局,提高生产效率,降低生产成本。
关键词:生产物流系统;车间布局;优化设计;系统布置设计
在物流快速发展的21世纪,生产物流的开展越来越受到人们的注重。随着汽车的普及,制造企业的生产物流也逐步成为社会关注的焦点。然而汽车生产规模逐渐扩大,生产物流落后的矛盾就日益突出,主要表现为高效的汽车生产系统与低效的生产物流系统不相适应。车间布局在设施规划与设计以及物流系统设计分析中都占据主导地位,车间布局优化更是能够充分利用人力资源,提高设备利用率,实现安全高效的生产活动。本文采用系统布置设计方法对某汽车总装车间布局进行设计优化,分析各作业单位之间的物流关系和非物流关系,结合综合关系相关图,合理布置生产物流系统,运用加权因素比较法,从物流作业效率、空间利用率、柔性空间布局等方面对布置设计方案进行评价,得出较优方案,从而提高生产效率以及空间利用率,为企业降低更多成本。
1 汽车总装车间布局的优化设计
1.1 物流关系分析
对汽车总装车间生产过程中各作业单位上的物流量进行分析,根据各作业单位对物流强度划分五个等级:A、E、I、O、U,其中,A、E、I、O分别占总作业单位对的10%、20%、30%、40%,U级代表那些无物流量的作业单位对。对总装车间各作业单位之间的物流强度进行分级,物流强度分析表如表1所示。
各作业单位之间除了物流关系还要考虑非物流关系,主要包括物料流动和信息流动之间的关系,操作环境与安全方面需保持的关系,同一部门的作业区域布置,功能相近的区域布置。非物流关系按各作业单位之间的相互密切程度划分为A、E、I、O、U、X六个等级。
1.2 作业单位分析
根据作业单位之间的物流与非物流关系进行加权计算,得出各作业单位的综合相互关系。根据总装车间的实际运量,确定物流关系与非物流关系的相对重要性的比值为3∶1,取A=4,E=3,I=2,O=1,U=0,X=1,计算得到各作業单位综合相互关系计算表,在此基础上,绘制出作业单位综合相关图。结合各工序的实际占地面积,以及工艺要求和设备的影响和限制,对总装车间进行优化重排,最后得出两种较优的布置方案,方案甲如图1、方案乙如图2所示。
1.3 布置方案评价
运用加权因素比较法对甲乙方案进行评价。按照各因素的相对重要程度,规定相应的权数,并排出各个备选方案的排队等级数,将各因素的排队等级数与权重的乘积相加得总分,该总分数即表明了各个备选方案相互比较时的优劣程度。通过计算方案乙优于方案甲,所以选用乙方案作为总装车间布局优化的方案。实践表明,企业根据方案甲对车间布局进行优化重排后,物流运输畅通,管理效率显著提高,为企业节约了很多的人力成本和经营成本。
2 结语
本文运用系统布置设计方法对某汽车总装车间进行了设施布局优化设计,通过对作业单位之间的物流与非物流关系的分析,得到了各作业单位之间的综合关系相关图,并提出两种优化车间布局的改善方案,最后运用加权因素比较法对两种布置方案进行评价,从而得到最优设计方案。实践表明优化方案极大地提高了空间利用率,改善了工作环境安全系数,增强了管理的方便性。
参考文献:
[1]周鑫.基于SLP和Flexsim的车间设施布置改善设计[J].机械制造与自动化,2010,03:4246+97.
[2]李琴,李泽蓉.某生产车间物流设施布置分析与设计[J].现代制造工程,2011(8):6769.
[3]王海瑶.SLP法在某铝业公司总平面布置中的应用[J].机械制造与自动化,2011,(5):6769.
[4]陈泽民.基于SLP方法的铁路物流中心布局规划研究[D].长沙:中南大学,2012.
[5]方庆琯,王转.现代物流设施与规划[M].机械工业出版社,2013.
[6]胡立涛,柯志红.基于SBMSLP 实施单元生产的混合车间布局研究[J].机械,2013,06:812.
CONTATC
重庆市渝中区中华路1号LG层LG13号81#
15923339397
2248511017
qifei1899
微信二维码
Copyright © 2002-2018 重庆启飞汽车设计有限公司版权所有渝ICP备18000729号 电话:15923339397