启飞汽车
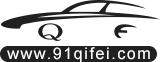
启飞汽车设计汽车设计— 国内专业产品设计培训基地!咨询热线:+86-15923339397
为中小型企业汽车研发和制造提供解决方案
专业承接整车设计开发项目
为各大主机厂,高校提供专业专项培训
为设计爱好者、毕业生提供专业系统培训
2019-04-11182作者:启飞汽车设计
摘要
汽车冲压模具在汽车零部件的制造过程中应用较多,在使用过程中一旦出现问题,不仅会影响模具使用寿命,还会影响冲压制件的表面质量。因此合理有效运用表面处理工艺来改善和提高汽车冲压模具表面性能是很有效的方法。
一、气相沉积法
气相沉积法主要有物理气相沉积法(PVD)和化学气相沉积法(CVD)。PVD是在真空条件下进行的,通过采用不同的物理方法,将待沉积的材料气化,将得到的分子、原子或离子沉积到基体材料表面。按照气化机理的不同,PVD主要包括真空蒸镀、溅射镀膜和离子镀膜3种基本方法。
真空蒸镀设备操作简单,沉积速度快,但是因气化离子的动能低,镀层与基体的结合力较弱,且高熔点物质和低蒸汽压物质(如Pt、Mo等)的镀膜制作困难。溅射镀膜由于气化粒子的动能大,故镀膜致密,与基体的结合力高,缺点是镀膜沉积速度较慢、设备昂贵。离子镀膜过程中参与沉积不仅有原子和分子,还有一部分能量较高的离子一起参与成膜,这就很大程度上提高了膜层与基体之间的结合力。但是受到蒸发源的限制,高熔点镀膜材料的蒸发镀较困难,而且设备复杂、昂贵。
CVD技术是一种热力学决定的高温热化学反应,它是利用气态的物质在固体表面上进行化学反应而生成固态沉积物的过程。CVD制备的膜层具有致密度高、气孔少、均镀性好及膜基结合力大的特点,性能相当优良。普通热CVD技术有一个很难避免的缺点就是过高的沉积温度(>1 000℃)。对那些不允许或不易于进行高温加热的基体材料(如严格控制变形的精密件),则必须采用辐射激发或放电激发的CVD技术,这种情况下制作的成本又被加大了。
二、化学镀
面对PVD法操作困难以及设备昂贵和CVD法必须在高温条件下进行的限制,目前还没有较为有效的解决方案。但除了CVD和PVD法以外,另外一种制膜技术──化学镀也越来越受到关注。早在19世纪40年代,Wutz用次磷酸盐在镍溶液中还原出金属镍,化学镀便开始发展。但化学镀真正的应用却是在100多年以后,1946年美国国家标准局的A.Brenner和G.Riddell利用化学镀的原理成功地在管子内部镀覆了Ni-P合金,该工艺自此走向了实际应用。例如,Ni-P-PTFE复合化学镀层具有良好的润滑作用,其不粘附的特性对模具脱模非常有利,特别是对于复杂形状的塑料压铸模具、橡胶模具都能起到很好的保护作用。
随着工业发展需求的提高,近年来还出现了将高硬度的颗粒与具有自润滑性的颗粒同时加入化学复合镀中的研究。比如将SiC和MoS2两种粒子同时加入Ni-P合金基质中,从而得到Ni-P-SiC-MoS2复合镀层。镀态时为非晶态结构,且复合镀层的硬度低于Ni-P-SiC而高于Ni-P-MoS2镀层。Ni-P-SiC-MoS2复合镀层摩擦磨损性能也比Ni-P-SiC镀层高,是一种具有良好自润滑性及耐磨性的优良复合镀层。另外,Ni-P-SiC-PTFE化学复合镀层也具有良好的耐磨性和自润滑性,但由于PTFE不耐高温,因此Ni-P-SiC-PTFE多元化学复合镀工艺主要用于塑料模具的表面处理。
化学镀也称自催化镀,施镀过程不需要电流,而是利用化学镀液中的氧化还原反应,还原出溶液中的金属离子(如镍离子、铜离子等),被还原后的金属会沉积在工件表面(工件表面必须具有自催化活性),从而形成镀层。化学镀从种类上可分为二元合金镀层、三元合金镀层以及加入第二相粒子获得的复合镀层。近年来化学复合镀技术不断发展,具有不同特性的粒子与基质金属组合参与。到化学复合镀过程中,便可以得到较好耐蚀性、较高硬度或者其他特殊性能的功能性镀层。粒子复合过程分以下几个阶段(图1)。
福利:做任何事情,都有方法。比如汽车行业如何最短时间内获取高薪,其实,是一件很容易的事情,结合汽车行业十多年工作经历,我做了一次系统全面总结无偿分享大家,文章共计十篇。帮助更多的网友在汽车行业快速发展。同时,我业余时间整理一套免费经典的CATIA视频教程, 汽车设计领域必备软件工具,大家有需要的,可以给我留言,请加微信qifei1799。提“启飞”就可以获取下载链接:汽车行业快速突破月薪过万绝密分享和catia视频精品一套。明确方向,精准学习,为以后在汽车行业职场做好铺垫。
CONTATC
重庆市渝中区中华路1号LG层LG13号81#
15923339397
2248511017
qifei1899
微信二维码
Copyright © 2002-2018 重庆启飞汽车设计有限公司版权所有渝ICP备18000729号 电话:15923339397