启飞汽车
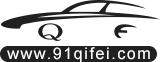
启飞汽车设计汽车设计— 国内专业产品设计培训基地!咨询热线:+86-15923339397
为中小型企业汽车研发和制造提供解决方案
专业承接整车设计开发项目
为各大主机厂,高校提供专业专项培训
为设计爱好者、毕业生提供专业系统培训
2019-03-11126作者:启飞汽车设计
摘要
以某车型左右后轮罩里板为研究对象,利用Auto Form软件建立有限元模型。首先确定板料形状,运用正交试验方法研究压边力、摩擦系数、拉延筋阻力对零件成形结果的影响,由正交试验的结果,得出了各因素对左右后轮罩里板成形结果影响大小依次为:压边力>摩擦系数>拉延筋阻力;最优参数组合为:压边力700k N、摩擦系数0.15,拉延阻力45N/mm。
一、有限元模型建立
汽车左右后轮罩里板呈圆盆形,型面曲率较大,空间曲面结构比较复杂,拉延成形过程中各部分深度变化较大。由于左右两部分基本对称,将左右两件合并在一起采用双件成形,再经过整形、修边、冲孔、翻边、冲侧孔、剖切等工序,最后将左右两轮罩剖开,既节省材料,又有利于拉伸成形,成形效果良好,最终获得合格制件。零件图如图1所示,零件长900mm,宽895mm,冲压深度最大值180mm,选用冲压材料DC05(特深冲用钢)。
图1 零件图和有限元模型
二、零件成形问题的研究
影响覆盖件成形性能的因素很多,要消除成形过程中出现的缺陷可以通过以下手段:(1)材料方面,根据成形缺陷重新选择毛坯材料来改变零件的成形性;(2)几何方面,调整模具几何参数,如改变模具间隙或模具圆角半径等;(3)工艺方面,改变坯料形状,调整压边力,调节拉深筋形状参数或改变摩擦等。
1.板料形状确定
根据零件形状初步选择1060mm×1065mm×0.8mm的矩形板料,在矩形板料的基础上根据零件形状又设计出2号和3号两种板料,板料形状及其成形模拟结果如图2所示。
由图可知,1号板料为方形,在冲压成形过程中四周板料会向中间移动,但是由于板料为方形,四个角落存在多余板料,这些多余板料会限制周围的板料向凹模口流动,随着拉延的继续,由于材料流动不充分,轮罩底部材料出现严重塑性变形,超过材料变形极限,出现破裂缺陷。2号板料是在1号板料的基础上切除4个边角,多余板料切除后成形结果有明显好转,但仍然存在拉裂区域。3号板料在2号板料的基础上进行修改,板料形状更接近于零件形状,消除了拉裂缺陷。但由于没有设置拉延筋,零件边缘存在大量起皱。从成形结果和节约材料两方面考虑选择3号板料。
图2 板料形状及成形模拟图
1.1压边力对成形质量的影响
压边力是影响工件成形的一个重要参数。由于压边力的存在,板料在模具和压料板之间流动时会产生摩擦力。这些摩擦力会通过影响材料流动的速度和方向从而实现对材料流动的控制。压边力过小,无法有效控制材料的流动,从而导致工件起皱;压边力过大,又容易导致工件被拉裂。针对初步模拟的压边力为基础进行调整,分别设定压边力为600kN、700kN、800kN、9000kN、1000kN五种工艺水平进行模拟。各水平下左右后轮罩里板拉延成形后的板料的最大增厚率和最大减薄率如表1所示。
表1 不同压边力下零件最大减薄率与最大增厚率
由表1可以看出,左右后轮罩里板成形时压边力应控制在600k N~800k N之间,在此区间板料成形过程中不会产生缺陷。但仅依靠压边力的大小来改善拉延成形质量并不能得到非常理想的效果。
2.摩擦系数对成形质量的影响
摩擦系数是影响板料成形结果的又一重要参数。板料和模具相互接触,当板料在冲压过程中流动时会与模具之间发生相对滑动,由于压边力的作用,在接触表面必然会产生摩擦,影响板料的流动。摩擦系数过大还会导致加工过程中模具表面温度升高加快,降低凸凹模的使用寿命;摩擦系数过小引起进料速度过快,易产生有起皱等缺陷的工件。将摩擦系数大小分别设置为0.13、0.15、0.17、0.19、0.21来观察摩擦系数对左右后轮罩里板成形结果的影响。其成形模拟结果如表2所示。
表2 不同摩擦系数下零件最大减薄率与最大增厚率
由表2结果可知,在板料成形时为了材料较好地流动,又不引起起皱等缺陷,左右后轮罩里板成形时摩擦系数应控制在0.15~0.19之间。
2.2拉延筋对成形质量的影响
拉延成形过程中,单一依靠压边力提供的阻力,模具和材料间的摩擦力很多时候还不够,而板料成形时又需要一定大小沿周边适当分布的拉力,这时就需要设置拉延筋。拉延筋的这一特点,使得它能在较大范围内控制板料的变形情况,从而避免起皱、破裂等多重冲压缺陷的产生。这里通过五组不同的参数来考究拉延筋阻力对左右后轮罩里板成形结果的影响。模拟时保证材料的基本属性参数不变,拉延筋阻力大小分别设置为0、45N/mm、95N/mm、145N/mm、195N/mm。其成形模拟结果如表3所示。
表3 不同拉延筋阻力下零件最大减薄率与最大增厚率
由表3结果可知,左右后轮罩里板成形时拉延筋阻力应该控制在45N/mm~145N/mm之间,在此区间板料成形情况最理想,不易产生拉裂、起皱等缺陷。
三、成形仿真优化
通过单因素分析可知压边力、摩擦系数、拉延筋阻力是影响板料成形最大增厚率和最大减薄率的主要因素。选择压边力、摩擦系数、拉延筋阻力作为主要影响因素,将Z=X(最大增厚率)+Y(最大减薄率)作为综合评价指标,最优化的成形模拟结果为Z值最小。每个因素设计3个水平,选用L9(34)正交表,正交试验安排见表4,试验结果见表5。
表4 正交试验因素水平
由极差R分析可知:RA>RB>RC,各因素对冲压成形结果的影响程度大小为A>B>C,压边力>摩擦系数>拉延筋阻力。根据Z值最小,成形结果最优,因此左右后轮罩里板成形结果最优的各因素最佳组合为A2B1C1,即压边力700k N、摩擦系数0.15,拉延筋阻力45N/mm。最优组合参数下的左右后轮罩里板成形极限图和厚度变化图如图3、图4所示。
图3 成形极限图
图4 厚度变化图
四、结论
(1)通过分析模拟实验结果可知,压边力、摩擦系数、拉延筋阻力对汽车左右后轮罩里板的成形结果都有较大影响。对汽车左右后轮罩里板成形最为有利的各因素取值范围分别为:压边力大小取值范围为600k N~800k N,摩擦系数大小取值为0.15~0.19,拉延筋阻力大小取值为45N/mm~145N/mm。
(2)通过正交试验挑选最优参数组合,将最大增厚率与最大减薄率之和作为正交试验的评价指标。由正交试验结果,得出各因素对左右后轮罩里板成形结果影响大小依次为:压边力>摩擦系数>拉延筋阻力。最优参数组合为:压边力700k N、摩擦系数0.15、拉延阻力45N/mm。最优结果的最大增厚率为8.1%,最大减薄率为20.8%。此时零件基本都处于安全部分,没有拉裂区域,有极少部分拉裂倾向区域和起皱区域,但不影响零件使用。
作者:何应威 朱兴元 来源:锻压装备与制造技术
福利:做任何事情,都有方法。比如汽车行业如何最短时间内获取高薪,其实,是一件很容易的事情,结合汽车行业十多年工作经历,我做了一次系统全面总结无偿分享大家,文章共计十篇。帮助更多的网友在汽车行业快速发展。同时,我业余时间整理一套免费经典的CATIA视频教程, 汽车设计领域必备软件工具,大家有需要的,可以给我留言,请加微信qifei1799。提“启飞”就可以获取下载链接:汽车行业快速突破月薪过万绝密分享和catia视频精品一套。明确方向,精准学习,为以后在汽车行业职场做好铺垫。
CONTATC
重庆市渝中区中华路1号LG层LG13号81#
15923339397
2248511017
qifei1899
微信二维码
Copyright © 2002-2018 重庆启飞汽车设计有限公司版权所有渝ICP备18000729号 电话:15923339397