启飞汽车
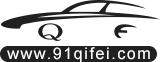
启飞汽车设计汽车设计— 国内专业产品设计培训基地!咨询热线:+86-15923339397
为中小型企业汽车研发和制造提供解决方案
专业承接整车设计开发项目
为各大主机厂,高校提供专业专项培训
为设计爱好者、毕业生提供专业系统培训
2019-03-06161作者:启飞汽车设计
摘要
以某一汽车轮侧内板为研究对象, 研究其成形所需工艺, 并使用Autoform软件进行仿真建模, 对其成形过程进行模拟分析。分析了各工艺参数对汽车轮侧内板零件成形的影响, 预测了板料成形过程中可能存在的起皱、拉裂和成形不足等缺陷, 通过将压边力从300 k N增大到800 k N, 并将拉延筋系数由0.6减小到0.5等设置, 消除了成形过程中的起皱和拉裂等缺陷, 零件表面质量控制在合格要求之内。最后按软件仿真进行实冲试验, 所得零件和仿真结果基本一致, 证明了仿真结果的准确性。利用优化后的方法, 零件已批量生产, 大大节省了试模成本和时间。
一、零件成形工艺分析
汽车轮侧内板零件如图1所示, 零件形状复杂, 表面由很多曲面组成, 有较多孔洞且方向不一致。选用DC04钢作为材料, 材料参数如表1所示。
图1 汽车轮侧内板零件
表1 DCO4钢材料参数
根据零件的特点, 设置为一模两件, 有利于板料均匀流动, 同时可以节省模具成本, 零件成形工序如下:
(1)拉延;(2)修边、冲孔;(3)翻边、整形;(4)冲孔、侧冲孔、侧修边、分离。在所有工序中, 拉延对零件成形至关重要, 主要的拉裂和起皱缺陷产生在这一工序, 因此, 对拉延进行仿真分析, 发现问题并进行调整工艺参数来规避缺陷。
二、Autoform仿真和分析
1.拉延方向确定
拉延方向在冲压过程中有着重要作用, 采用正确的拉延方向才能获得理想拉延件, 并且拉延方向对后续工序的安排有重要影响。确定拉延方向时, 首先, 保证应一次将板件拉延出, 无死角。确保凸模和凹模可以顺利闭合, 在开始拉延时凸模与毛坯接触状态良好, 且接触面应尽量大, 同时应保证拉延深度均匀。最终确定的拉延方向如图2所示。
图2 拉延方向
2.工艺补充面和压料面形状确定
将零件通过UG导出成IGES格式, 并导入Autoform软件。使用软件对数模自动进行网格划分, 也可调节网格精度来达到较高计算精度。本次采用默认精度进行仿真, 在建模生成器中进行拉延建模。在Process中添加Empty plan, 床台选择默认, 手动添加Draw20, 单动拉延。分别进行空洞填补, 确定拉延方向, 调整分模线、圆角等来生成压料面和工艺补充面。工艺补充面应尽量小, 在拉延完成后需切除。压料面和工艺补充面如图3所示。
图3 工艺补充面和压料面
3.拉延筋设置
板件成形中, 拉延筋有着不可忽视的作用。拉延筋影响板料进料速度, 控制进料是否均匀, 控制拉延筋可以较好地控制板件缺陷。在仿真过程中, 若采用真实拉延筋需要设置复杂参数, 需要较多时间来进行计算, 效率较低。因此, 通常使用等效拉延筋来代替, 根据拉延筋系数设置, 可承担一定的力。等效拉延筋实则为一条线, 通过设置线的阻力系数来达到真实效果。通过等效代替, 可以在保证计算精度的前提下大大节省仿真所需要的时间。拉延筋设置如图4所示, 添加4根拉延筋, 系数为0.6。
图4 拉延筋设置
4.成形过程分析
本次轮侧内板件为小批量生产, 使用方便, 节省落料模具成本, 直接使用切料机切料。板料厚度设为1.4 mm, 大小为910 mm×700 mm。凸模Die、压边圈Binder、凹模Punch的距离采用软件默认, 因为在仿真过程不影响成形性能, 故不做修改。初步设定压边力为300 k N, 其他参数默认。拉延工具体位置如图5所示, 成形过程中, 板料放置在压边圈上, 下模不动, 上模下行, 与压边圈夹紧板料后一起下行与下模合模, 完成零件成形过程。
图5 拉延工具体初始位置
分别设置压边力为300, 400, 500, 600, 700和800 k N, 成形过程如图6所示。由图6a~图6e可知:
(1)随着压边力增大, 起皱区域越来越小;
(2)在压边力为700 k N时出现了拉裂风险区, 到800 k N时出现拉裂;
(3)在800 k N时起皱区域最少, 零件上表面已经接近理想状态。
图6 各压边力下的成形图 (a)300kN (b)400kN (c)500kN (d)600kN (e)700kN (f)800kN
因为受拉延筋影响, 板料流动阻力大, 造成拉裂, 所以, 修改图6f中拉延筋 (2) 系数为0.5, 得到其成形图、FLD图、减薄图和起皱图, 如图7所示。
图7 修改拉延筋后的数据图 (a)成形图 (b)FLD图 (c)减薄图 (d)增厚图
对于汽车内覆盖件, 若减薄率大于30%, 则认为拉裂, 增厚率大于10%, 则认为起皱。本坯料厚度为1.4 mm, 因此, 认为只要零件厚度大于0.98 mm (即减薄量小于0.42 mm) , 厚度小于1.54 mm (即增厚量小于0.14 mm) , 即认为零件合格。由图7可知, 零件成形性能很好, 无破裂区域, 零件最薄处为1.107 mm, 减薄率为20.9%, 小于30%, 零件最厚处为1.46 mm, 增厚率为4.36%, 小于10%, 符合零件要求。
三、试验
根据模拟结果制造了模具, 并进行试模。拉延零件如图8a所示, 对拉延零件进行质量检查, 发现该零件无拉裂和起皱缺陷, 最终成形的汽车轮侧内板实物如图8b所示。将实际成形零件和有限元软件模拟结果进行对比, 得出模拟结果和试验基本吻合, 表明本文建立的有限元模型的正确性, 仿真模拟可用于指导生产。
图8 试验得到的零件 (a) 拉延成形的零件 (b) 最终零件图
四、结论
(1)本产品为对称件, 常使用共模方法生产, 方便冲压, 节省成本。
(2)针对某车轮侧内板, 使用有限元仿真, 得到效果很好的板料和板料位置, 包括压边力大小等参数, 用于指导实际试模。
(3)板料是否选用弧形板料要根据产量与成形性来看, 本产品小批量生产, 优先选用方形板料, 节省落料模具成本, 且成形性较好。
(4)成形效果与试模结果基本一致, 无拉裂和起皱缺陷, 符合零件生产要求, 验证了本文仿真建模的准确性, 可指导生产。
作者:陈保全 李国强 顾强 陈明 陈炜 来源:锻压技术
福利:做任何事情,都有方法。比如汽车行业如何最短时间内获取高薪,其实,是一件很容易的事情,结合汽车行业十多年工作经历,我做了一次系统全面总结无偿分享大家,文章共计十篇。帮助更多的网友在汽车行业快速发展。同时,我业余时间整理一套免费经典的CATIA视频教程, 汽车设计领域必备软件工具,大家有需要的,可以给我留言,请加微信qifei1799。提“启飞”就可以获取下载链接:汽车行业快速突破月薪过万绝密分享和catia视频精品一套。明确方向,精准学习,为以后在汽车行业职场做好铺垫。
CONTATC
重庆市渝中区中华路1号LG层LG13号81#
15923339397
2248511017
qifei1899
微信二维码
Copyright © 2002-2018 重庆启飞汽车设计有限公司版权所有渝ICP备18000729号 电话:15923339397