启飞汽车
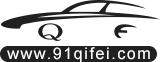
启飞汽车设计汽车设计— 国内专业产品设计培训基地!咨询热线:+86-15923339397
为中小型企业汽车研发和制造提供解决方案
专业承接整车设计开发项目
为各大主机厂,高校提供专业专项培训
为设计爱好者、毕业生提供专业系统培训
2018-11-20151作者:启飞汽车设计
摘要
分析了汽车离合器减振盘的工艺性, 介绍了一种工序少、效率高、质量稳定的复合冲压工艺以及CAE仿真技术在冲压开发中的应用, 针对现有工艺的缺陷, 设计了更合理的工艺流程, 结合计算机仿真技术, 建立了工艺仿真模型。根据仿真结果, 对可能存在的工艺缺陷提出了改进方案, 试模结果表明, 改进后的工艺对生产效率和零件成形质量改善效果明显。
一、零件结构
离合器减震盘属于冲压件, 形状较为复杂, 成形与分离工序多, 精度要求高, 材料为SPHE, 厚度为3.0 mm, 在一个圆形板料上均布9个敞口凸包, 并在平面上成形一圈加强筋, 另有若干铆接销孔, 平面度为0.2 mm, 铆接销孔位置度为0.3 mm, 边线平整无毛刺, 圆度为0.3 mm, 外观无明显压印、裂纹, 减振盘结构如图1所示.
对于该类圆形零件的冲压, 传统工艺采用先落料, 再加工其他特征的方案, 冲压流程为:落料、冲孔→冲销孔、方孔→冲窗口→窗口成形→压筋→修边, 工艺流程如图2所示。该工艺方案工序较多, 生产过程定位误差大, 零件成形质量难控制。由于窗口成形和压筋的安排, 对板料的周边材料有较强的拉伸作用, 影响周边小圆孔和方孔的冲裁质量。
图1 减振盘结构
现通过整合工序, 抑制材料流动等方法, 避免了材料流动带来的风险, 稳定了零件的冲孔质量, 有效地提高了生产效率。
图2 工艺流程
二、工艺方案
经过对离合器减震盘的工艺分析, 改变原来的工艺方案, 采用3道复合工序进行生产。
1.冲窗口与下方料
OP10为成形前的下料工序, 包括凸包成形需要的预冲窗口。传统工艺中一般采用整体落料, 需要在材料上设计工艺搭边, 增加了材料成本, 同时冲裁边线大, 对生产设备的冲裁力要求也较高。
鉴于无论采用何种方式落料, 经拉深成形后零件的边界都会变化, 后序还需修边工序, 故对落料工序进行简化, 用单边剪板的方式代替整圈落料。同时考虑生产的方便, 采用连续落料的方式使生产效率最大化, 零件排样如图3所示。
图3 零件排样
在生产时, 以初始定位销定位料边, 第一步先冲出工艺孔, 完成第一步后继续送料, 再以工艺孔定位, 冲出窗口, 同时将料片从条料上剪出, 完成OP10。在OP10的设计中, 集成了冲孔和落料2个工序, 总冲裁周长为1 535 mm, 冲裁力F落=KLtσb=1.1×1 535×3.0×410=2.08×106N, 卸料力:F卸=k F落=0.03×2.08×106=6.24×104N。选用2.5×106N的压力机、10个MQQ6.0-015-085强力型氮气弹簧, 可以满足工艺要求。
2.压筋与成形
该工序以中孔和工艺孔定位, 卸料板兼压筋, 属于常规钣金成形工艺, 如图4所示。难点是工艺孔位置的设计, 需确保成形过程中的材料流动不会影响工艺孔的位置和尺寸。如果设计不当, 将导致后面工序的模具定位失效。
图4 成形工序
3.修边与冲孔
成形工序完成后, 零件已基本定形。最后工序将零件与周边废料分离, 同时将所有孔冲出, 如图5所示。总冲裁周长为952 mm, 冲裁力F冲=KLtσb=1.1×942×3.0×410=1.274×106N, 卸料力:F卸=k F冲=0.03×1.274×106=3.82×104N。选用2.5×106N的压力机、8个SJB40×20×64强力压缩弹簧, 可以满足工艺要求。
三、成形工艺仿真
工艺过程数值模拟选用钣金成形仿真软件Autoform。按实际设计的工艺数据建立分析模型, 如图6所示。
设定好工艺及材料参数后提交运算, 模拟结果如图7所示。从成形效果可以看出, 窗口处的压筋成形没有对工艺孔造成拉伸影响, 可以按此效果确定工艺孔的位置。窗口拐角处显示材料有起皱趋势, 由于该零件属于厚板挤压成形, 局部的材料加厚在实际生产中不会产生明显起皱现象。
图5 修边冲孔工序
图6 分析模型
图7 模拟结果
除了验证材料的成形性外, 材料的变薄率也是十分重要的指标, 该工艺的成形减薄率如图8所示。从图8可以看出, 零件在窗口拐角成形处存在开裂风险。按生产经验, 这样的减薄率在类似成形工艺中十分危险。针对拐角处的开裂情况, 需要在模具结构设计时对成形凹模进行优化处理, 优化模具结构设计如图9所示。
图8 成形减薄率
图9 优化后的凹模
通过在拐角处设计工艺避位, 增加拐角处的成形间隙, 改善材料的流动, 避免材料减薄, 从而阻止开裂。通过计算机仿真分析, 该复合工艺整体可行。对可能存在的技术问题也在设计时得到了解决, 避免了返工返修带来的麻烦和浪费。
四、工艺验证
复合工艺的投入使用对现场的生产状态改善明显。若按单工序工艺生产, 原工艺采用7道单工序生产, 效率低, 且成形工序与冲孔工序安排不合理, 成形后将铆接销孔拉变形。而采用复合工艺后工序缩减一半, 生产效率更高, 零件生产质量更加稳定, 降低了物料和模具的运转频率, 也减轻了对人员和设备的依赖, 同时也简化了物料和模具的管理, 复合工艺如图10所示。
图1 0 改进后的复合工艺
五、结束语
只要模具空间和材料的成形极限允许, 冲压件可以按“落料—成形—修边冲孔”模式进行工艺设计。该项目通过合理整合工序, 为今后类似冲压零件的工艺设计进行了尝试, 对同类零件的复合冲压工艺设计具有借鉴意义。
作者:蒋件生 吴天生 来源:模具工业
福利:做任何事情,都有方法。比如汽车行业如何最短时间内获取高薪,其实,是一件很容易的事情,结合汽车行业十多年工作经历,我做了一次系统全面总结无偿分享大家,文章共计十篇。帮助更多的网友在汽车行业快速发展。同时,我业余时间整理一套免费经典的CATIA视频教程, 汽车设计领域必备软件工具,大家有需要的,可以给我留言,请加微信qifei1799。提“启飞”就可以获取下载链接:汽车行业快速突破月薪过万绝密分享和catia视频精品一套。明确方向,精准学习,为以后在汽车行业职场做好铺垫。
CONTATC
重庆市渝中区中华路1号LG层LG13号81#
15923339397
2248511017
qifei1899
微信二维码
Copyright © 2002-2018 重庆启飞汽车设计有限公司版权所有渝ICP备18000729号 电话:15923339397