启飞汽车
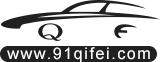
启飞汽车设计汽车设计— 国内专业产品设计培训基地!咨询热线:+86-15923339397
为中小型企业汽车研发和制造提供解决方案
专业承接整车设计开发项目
为各大主机厂,高校提供专业专项培训
为设计爱好者、毕业生提供专业系统培训
2018-10-1978作者:启飞汽车设计
摘要
随着汽车的不断普及, 开闭件系统作为汽车中直接影响用户使用的部分, 得到了较快的发展。特别是用户对汽车的需求, 已经逐步从单一的代步向生活空间的一部分转化, 对开闭件系统的要求也越来越高, 这些需求更加激发了开闭件系统设计的进步, 使开闭件系统在开发流程、设计方法、验证手段等方面, 形成了一套较为完备和独立的体系。
汽车开闭件包含了可以开闭的车身构件, 例如发盖、车门和行李箱盖。汽车开闭件是车身的关键运动件, 其灵活性、坚固性、密封性等方面的特点, 对汽车产品的使用质量有重要的影响。因此, 对汽车开闭件的开发流程、设计方法及验证手段进行探究, 对于提升汽车品质有着十分重要的意义。
一、开发流程
汽车开闭件系统的开发流程, 可大致分为前期分析、工程设计、后期分析、实车验证、产品定型等五个阶段。
1.前期分析
汽车开闭件系统的前期分析, 首先是参考车、竞争车的解析对标, 形成相应的数据库, 作为重要的设计参考。根据所开发车型的市场和用户群定位, 以及造型主题, 确定关键零部件的初步技术方案, 包括结构形式、装配状态、通用化、DFMEA等方面在内的设计思路。
根据初步的技术方案, 应对所涉及的零件进行涉及成本的VA/VE分析, 确定低成本方案, 以及是否需要引进低成本供应商的结论性分析。同时, 还要根据初步的技术方案, 向造型输入设计硬点, 特别是影响造型的相关零件数据。
在市场部门的产品调研、造型部门的创意草图和重要硬点的总布置完成后, 最终确定关键零部件的技术方案, 包括详细的设计思路、技术开发要求、DFMEA等。
在造型效果图、CAS面、模型、A面完成后, 应对其在零部件布置、制造工艺性、质量控制等方面进行分析, 并向造型反馈分析结果, 跟踪问题的解决情况, 另外还应在模型制作前提出外观间隙断差要求, 在模型冻结时, 涉及外观的初步主断面应同时冻结。
2.工程设计
工程设计阶段的工作并不仅仅限于3D数据的设计, 更多的是2D数据和相关技术文件的编制, 主要包括公差定义、技术条件、产品特性清单等。
3D数据体现的是零件的外观、结构和装配关系, 详细的尺寸、公差应通过2D图来定义。2D图应根据零件的不同用途, 以及同一零件中不同区域的功能, 对尺寸和公差进行合理定义, 既要避免因公差偏大而造成的装配和使用误差, 又要避免公差偏小而造成的不必要的制造要求。
3.后期分析
在工程数据发布后, 应通过软件模拟的手段, 对设计数据进行验证, 主要包括DMU检查、CAE分析和SE分析三个部分。
DMU检查即电子样车单元检查, 是指将全车数据装配成一个整体, 对相互之间的装配、间隙等关系, 以及运动轨迹、包络进行检查。
CAE分析是对整车零件进行网格划分, 利用有限元方法, 对碰撞安全、车体结构性能、开闭件刚度、整车模态、NVH等方面进行计算机模拟分析。
SE分析是借助工艺成形软件及工艺人员的实际经验, 对整车零件的工艺性进行详细分析, 包括冲压、焊接、涂装、总装四大工艺的检查。
4.实车验证
实车验证包括两个重要组成部分, 样车装配和试验验证。
样车装配过程中, 可以对开闭件系统的装配关系、运动轨迹、公差设计等方面进行充分验证, 这一阶段出现的问题, 都应反馈回设计上进行仔细检查, 由此判断是设计问题、工艺问题还是质量问题, 从而进行有目的性的整改。
开闭件系统的试验主要包括疲劳试验、刚度试验等台架试验, 以及作为整车的组成部分, 进行碰撞、NVH等试验。试验是对CAE分析结果的进一步验证, 同时也对工程设计、样车装配、零件质量提出进一步的改进方向。
5.产品定型
经过实车验证合格后的产品, 随着整车开发项目通过投产签署, 应进入产品定型阶段。产品定型阶段的工作主要包括数据归档、技术文件编制及归档等。
归档的数据包括主断面图、3D、2D、技术条件, 应按统一的要求进行归档, 并确保数据的可读性和正确性。
二、设计方法
从开发思路上来看, 开闭件的设计方法分为正向和逆向两种形式。
1.正向设计
正向设计是通过CATIA等设计软件, 全新地设计零件的结构形式、装配关系, 由此确定零件的尺寸公差、性能要求、材料要求等。
正向设计的灵活度高, 可以根据不同车型的要求和实际的装配环境, 设计出满足该车型和环境所要求的零件, 但由于是全新设计, 不仅周期长, 而且设计可靠性较低, 依赖于设计人员的经验和水平, 同时要通过相关的试验进行验证, 设计风险大, 成本高。
2.逆向设计
逆向设计是通过扫描现有的零件, 在计算机中形成点云, 并通过相应的软件 (如Surface等) 进行后期分析处理, 得到零件的结构形式、装配关系, 从而参考现成零件确定尺寸公差、性能要求、材料要求等。
逆向设计的周期短, 设计可靠性较高, 可以减少甚至取消相关的试验, 设计风险小, 成本低, 但其灵活度低。由于受到车型和装配环境的限制, 可能会为了借用而影响到周边零件以及自身功能的充分发挥, 同时还存在专利侵权的隐患。
三、验证手段
开闭件系统的验证包括计算机验证和实物验证两大类。DMU、CAE、SE等计算机分析验证手段已经在前文有所提及, 这里仅对涉及开闭件系统的试验作简要介绍。
1.刚性试验
开闭件系统的主要刚性试验项目和评价标准如下:
(1)发盖扭转刚性试验:所测得的载荷—位移曲线图应连续变化无突变 (临界点除外) ;刚性指标应大于2000Nm/rad。
(2)门柱 (15°角和全开) 刚性试验:对于轿车车门, 当载荷为1000N时, 最大位移量应不大于8mm, 永久变形量应不大于0.5mm。
(3)车门窗框变形测量:所测得的载荷—位移曲线图应连续变化无突变 (临界点除外) ;当载荷为200N时, 位移量应不大于8mm。
(4)背门开启位置和锁止位置的扭转刚度:所测得的载荷位移曲线图应连续变化无突变;当载荷为50N时, 最大位移量应不大于6.00mm (开启) 和3.00mm (锁止) 。
2.疲劳试验
开闭件系统的疲劳试验主要项目和评价标准如下:
(1)发盖加力开闭、完全开闭和侧向加载疲劳试验:进行5000次开闭试验后发盖及各附件工作应良好;发盖和车身上无破坏、变形等现象。
(2)背门加力开闭和完全开闭疲劳试验:进行15000次开闭试验后背门及各附件工作应良好;背门和车身上无破坏、变形等现象。
(3)旋转门加力疲劳试验:试验后旋转门及各附件工作应良好;旋转门和车身上无破坏、变形等现象。 (玻璃全开25000次, 半开25000次) 。
(4)旋转门完全开闭疲劳试验:进行40000次开闭试验, 试验结束后前门及各附件工作应良好;试验中和结束后前门开关不应有异响;前门开门限位器不能有变形、损坏;扭矩不应下降;前门开关力变化在10%以内。
(5)旋转门边缘加载和垂直加载疲劳试验:进行50000次试验后旋转门及各附件工作应良好;旋转门、铰链立柱无破坏、变形等现象。
四、结语
开闭件系统的设计在整车开发过程中是一个相对独立但又非常复杂的工作, 本文只是简单的对其开发流程、设计方法、验证手段等方面进行了简单的概述。在开发过程中还有许多更具体更复杂的工作。在将来的开闭件开发中将采用模块化设计, 其具有减少装配时间, 在规模化生产中更节约成本、维修方便、结构简单等优点, 同时对零部件的设计、开闭件材料的开发提出来更高的挑战。
福利:做任何事情,都有方法。比如汽车行业如何最短时间内获取高薪,其实,是一件很容易的事情,结合汽车行业十多年工作经历,我做了一次系统全面总结无偿分享大家,文章共计十篇。帮助更多的网友在汽车行业快速发展。同时,我业余时间整理一套免费经典的CATIA视频教程, 汽车设计领域必备软件工具,大家有需要的,可以给我留言,请加qq:1011852705,微信qifei1799。提“启飞”就可以获取下载链接:汽车行业快速突破月薪过万绝密分享和catia视频精品一套。明确方向,精准学习,为以后在汽车行业职场做好铺垫。
CONTATC
重庆市渝中区中华路1号LG层LG13号81#
15923339397
2248511017
qifei1899
微信二维码
Copyright © 2002-2018 重庆启飞汽车设计有限公司版权所有渝ICP备18000729号 电话:15923339397